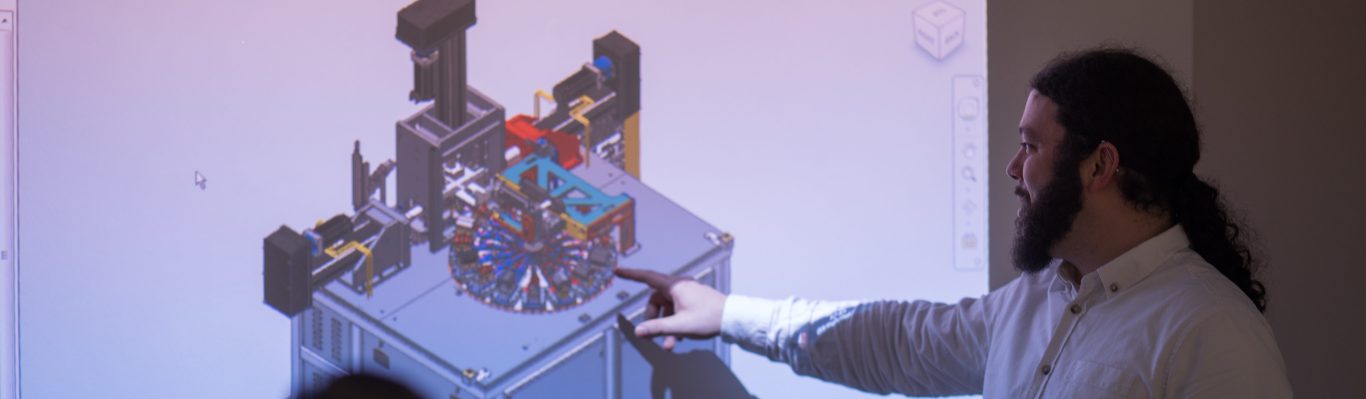
Custom Automation Solutions
End-to-end, custom automation solutions
Complete, custom, automation solutions, large and small
We operate as a close, trusted, automation partner to the world’s leading MedTech manufacturers, building complete, custom automation solutions, large and small, rolled out globally. Backed by a team of 170+ automation experts and recognised as a Tier one supplier, we’re responsible for full delivery, including planning, concept design, validation, build, install and after-sales service & support.
The team, expertise, and scale to deliver innovative, challenging solutions
-
Proven expertise.A 170+ strong team of automation experts, successfully delivering proven solutions to MedTech manufacturers for over 35 years.
-
Deep MedTech sector knowledge.GAMP 5 validation services, and protocols for regulated environments.
-
Vendor Flexible.Guiding and selecting the right solution for each process and application.
-
Uncompromising quality.All machines built to ISO9001:2015 for outstanding quality and reliability and capability to CE certify machines.
-
Technology driven.An engineering technology company developing smart machines using the latest technologies.
-
Advanced, large facilities.Super-modern, super-clean floor space of 100,000 sq. ft. The capacity to plan, build and test even the largest projects.
-
De-risking methodologiesDe-risk even the most complex of projects with our Proof of Principle (PoP) methodology.
-
Expert, seamless integrations.Integrating the latest OEM technologies and specialist equipment.
-
One partner for all.An end-to-end automation partner delivering design, build, validation, installation, certification and after-sales service and support.
Our Solutions
From small scale automation to the most complex solutions
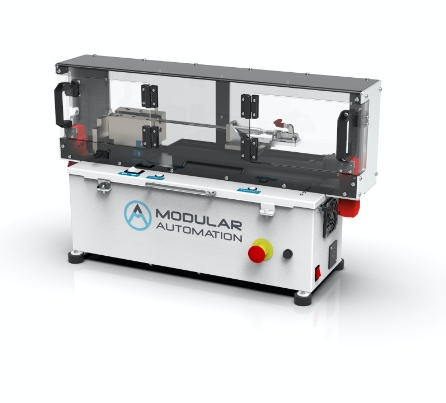
Bench Top Units / Semi-Auto
Single process, small-scale machines.
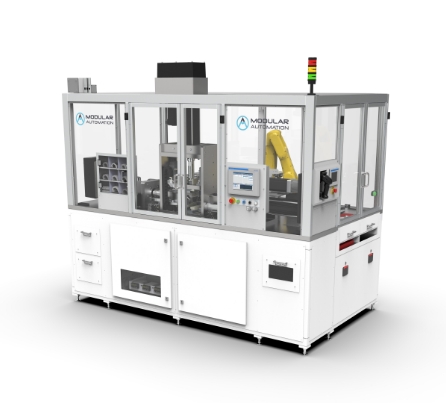
Custom Standalone Machines
Single or multi-process.
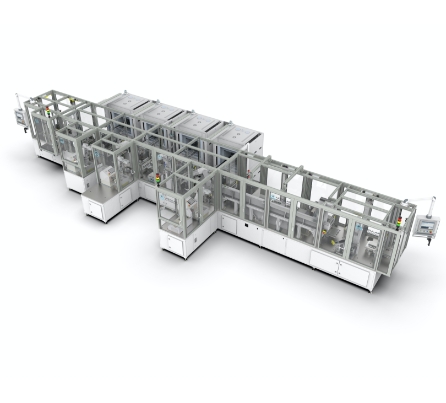
Multi-Zone Production Lines
Multi-zone machines for greater efficiency.
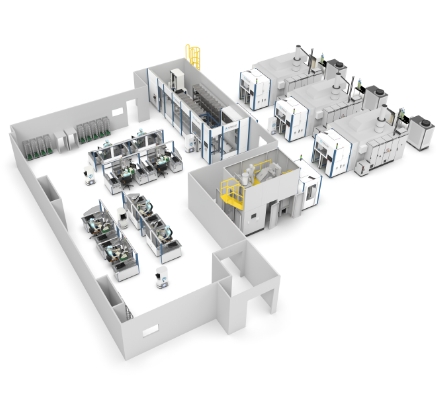
Large Scale Integration
Turnkey delivery of the most complex automation solutions.
How we do it
A step-by-step approach to deliver the right solution.
-
Understand the needs
We collaborate closely with our customers to understand their needs, with particular focus on the ROI they’re hoping to achieve, from reducing overheads and improving safety, to increasing capacity or throughput. -
Learn the processes
We learn and assess the processes our customer uses in manufacturing, including the materials, the products and the applications. -
Concept Development
A learning phase for both our customer and Modular, we develop a concept for the automation project, featuring the equipment or manufacturing line, helping to visualise the final implementation. The methodology helps to identifies the risks and feasibility of the project, providing greater clarity in terms of project execution, the equipment that will be used, how long it will take and what the overall budget will be. -
Proof-of-Principle
Our Proof-of-Principle (PoP) methodology is used to de-risk the processes identified at the Concept Development stage, prior to commencing the main project. This clarifies the approach, timeline and budget. It’s the final step to ensure the automation project will meet the needs of the customer exactly as intended. -
Final proposal
Once the Concept Development and PoP are complete, our team set out the final proposal for the delivery of the custom automation solution. -
Designing the system
A collaborative design effort between all functions in Modular to design the system as planned in the Concept Development & PoP phase. This stage includes multiple customer design reviews. -
Build & Debug
The final system is built and undergoes significant equipment testing, engineering runs and factory acceptance testing. -
CE certification and documentation
Comprehensive documentation with all equipment CE certified, typically meeting Category 3 PLd requirements. -
Final integration
Final install, commissioning and acceptance testing is completed onsite at the customer facility. This includes post-install support to ensure the solution is working as intended.
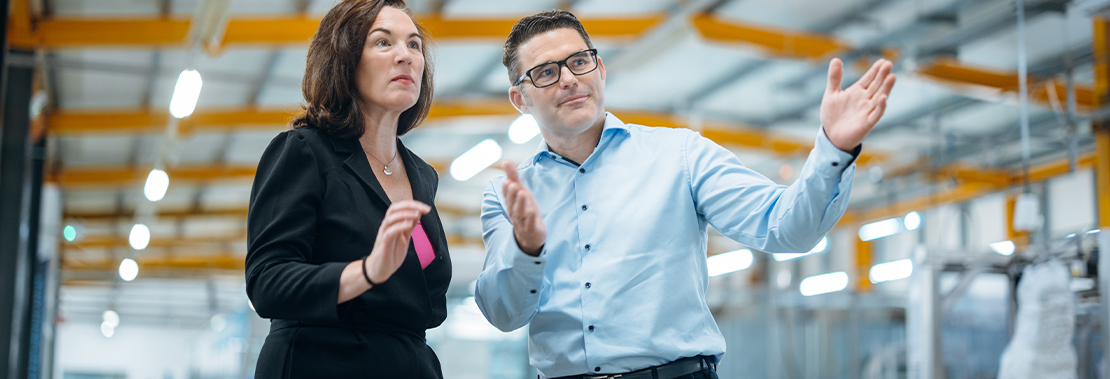
Why Modular for Custom Automation?
The longevity and experience to deliver innovative, challenging solutions.
For over 35 years our experts have planned, designed and built the most innovative, complex, challenging automation equipment solutions for MedTech manufacturers. We’ve never failed a customer. We always, always deliver.
Technology pioneers driving the most complex of integrations.
We’re an engineering technology company developing smart machines using the latest technologies. We take risks, we test, trial and explore new technologies, new innovations, new integrations. Always ready to use the latest, most advanced technologies to power innovation and integration. Allowing us to take on the most complex, challenging projects, and providing our customers with a competitive edge.
Deep collaboration is in our nature.
We are a multi-disciplined team with the capability, knowledge, passion, ingenuity and confidence to work shoulder-to-shoulder with the world’s most advanced MedTech manufacturers. We go deep to truly understand their needs, their processes, their materials, products and applications. Arming ourselves with the intel to deliver the right solution, every time.
Extensive knowledge of regulations, standards and protocols.
Experience of automation protocols for regulated environments including equipment installed into clean rooms (ISO class 7 & 8), ATEX & high temperature environments 200°C+ and sealed nitrogen environments. Computer system validation (CSV) to GEP/GMP regulations and qualification to GAMP requirements and our Software Development Life Cycle model (V-model).
One partner for all.
An end-to-end automation partner delivering design, build, GAMP 5 validation, on-site installation, CE certification to category 3 PLd requirements, and after-sales service and support.
High-quality, well-sourced, competitively priced supply chain.
An extensive, well-sourced, global supply chain of partners, suppliers, and vendors, allowing us to fulfil large orders at short notice for super competitive prices. A chain of proven, trusted partners, built for speed, scale and quality.
Each part fully documented for reference.
All parts are laser engraved with a part number and revision level for future reference. All logged in our ERP system, all fully traceable and available when needed.
De-risk with PoP. Enter full-scale development with confidence.
Our Proof of Principle (PoP) methodology is a quick, cost-effective mechanism used to eliminate project risks at the concept stage. Allowing for more accurate cost and development forecasts, this proven approach ensures our customers enter full-scale development with confidence that the project will deliver as intended.
The scale and capacity to deliver.
A team of 170+ automation experts. A super modern, super clean floor space of 100,000 sq. ft. Primed to take on the largest custom automation projects.
Case Study
Moving Automation Forward
In 2012 a longtime automation customer approached Modular with a challenge: they wanted to increase production output of their primary product by 30% and cut the footprint of the machine in half. Given that the product is highly specialised, with varying…
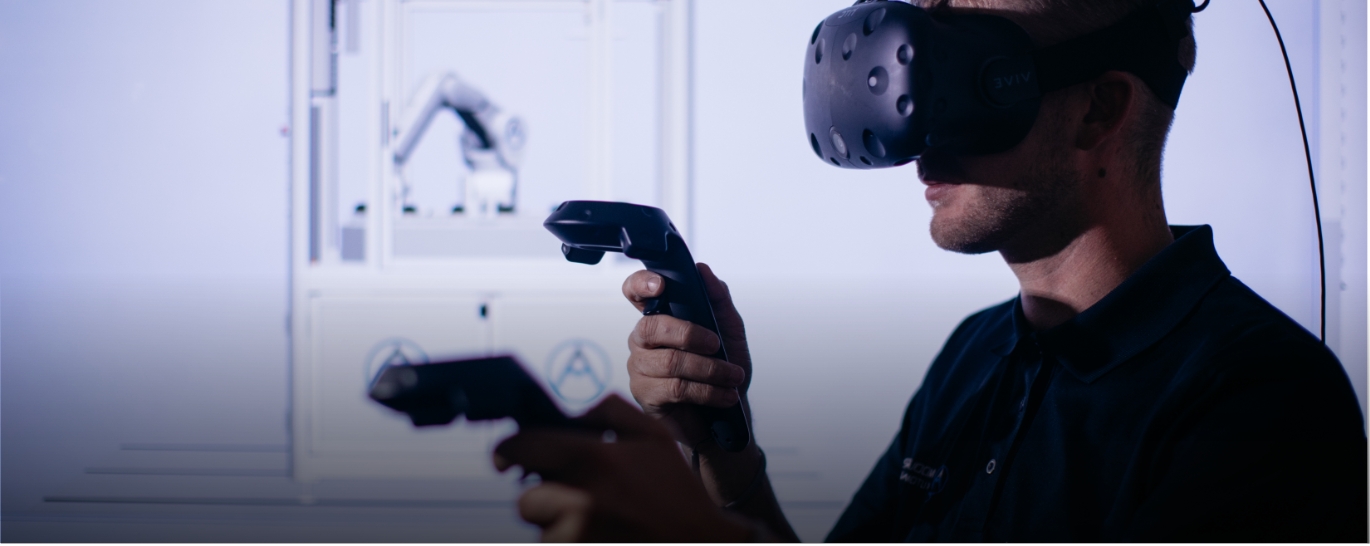
Let’s Talk
Tell us about your manufacturing challenge, and one of our senior engineers will be in touch to explore how we can help.
Contact Us